Technical service summary for Anshan Steel Plant in Sichuan
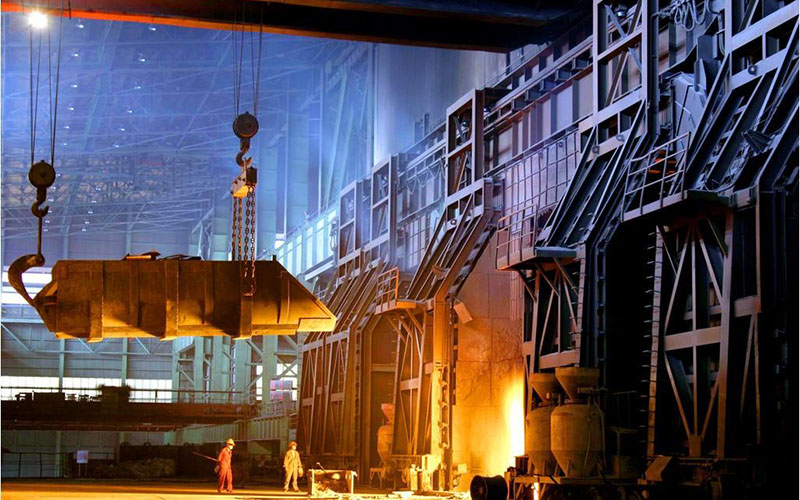
Preface
On July 29, 2019, the technical team reached an agreement with Sichuan Anshan Iron and Steel Co., Ltd. that the steelmaking technical team would help it optimize the process and improve the production capacity. Anshan Iron and steel company promised to use the furnace lining provided by our side.
Magnesia carbon bricks offered by our side will be carried out hot testing for EAF lining twice, Sichuan Anshan Iron and Steel Co., Ltd. (Party A) requires that the use times of EAF lining and ladle lining must exceed the previous refractory manufacturers’ use times of 350 heats (the requirement is that slag-line exchanging will not be allowed to do before whole lining life concluding). Before that, their historical maximum lining life was 312 heats (the slag line bricks were digged and repaired once during using time). according to equipment status of Sichuan Anshan Iron and Steel Co., Ltd, there is great promotion room over production capacity. In the meantime there are many problems such as power supply system, slag making process, oxygen supply system, rationality of oxygen lance and carbon lance installation, and lining laying technology. The equipment management is not in place, and the scrap treatment and classification management are far from the requirements of high production. After our on-site observation and investigation, the entire production process and on-site operation were analyzed in detail, and the corresponding improvement scheme was formulated.
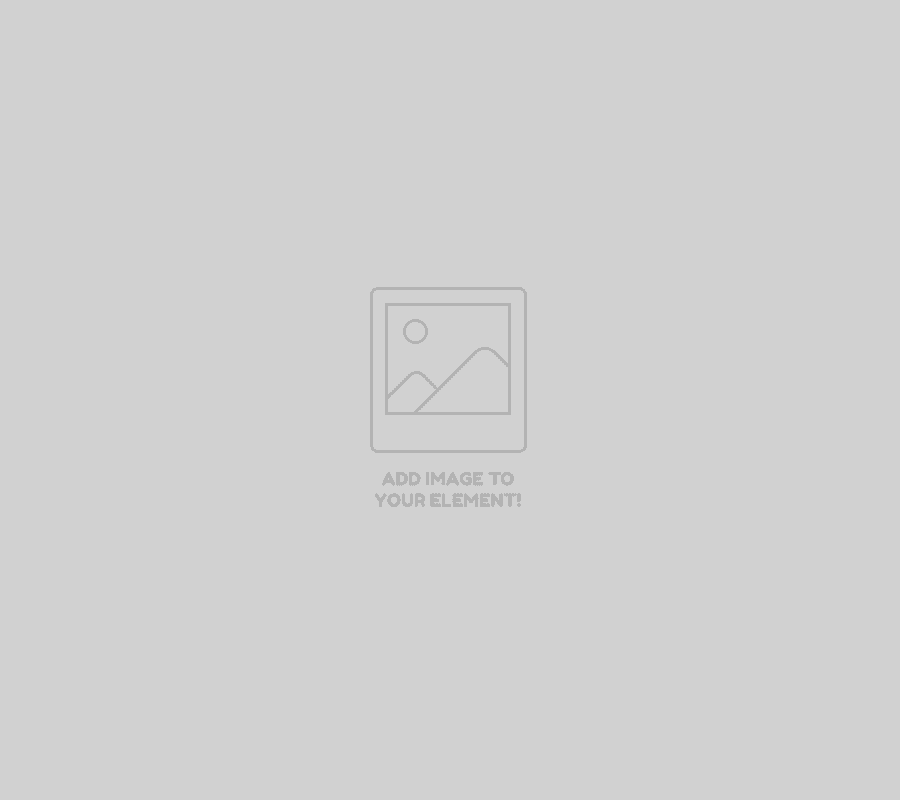
Situation of Sichuan Anshan Iron and Steel Co., Ltd in those days
1. The output was low, which didn’t get the output designed, and the annual production didn’t exceed 50000 tons yet.
2. High electricity consumption.
3. EAF lining life is short.
4. The service life of center block of EAF is very low.
5. The production cost is very high.
6. CCM is planned to be transformed. At that moment, the capacity of CCM didn’t match with that of EAF, which also affects the capacity improvement in a certain extent.
7. The failure rate of the rolling mill is high, which didn’t match the previous capacity; new rolling mill was being introduced.
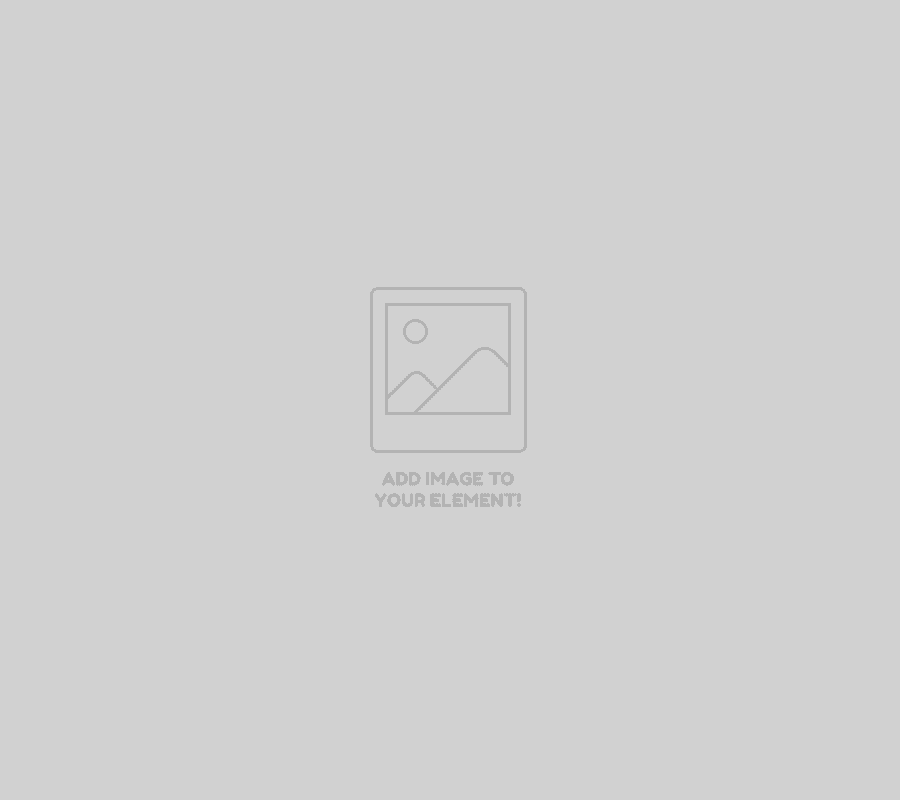
Taking improvement measures
1. Restored oxygen lance between charging inlet and EBT, and readjusted the installation angle of all oxygen lances.
2. A carbon lance was added between 2# electrode position and EBT to ensure need for foaming slag in whole process.
3. In order to make refractories consumption synchronously and prolong EAF lining life, strengthening local brick-cnstructing method in hot spot area is adopted, some of length 600 mm bricks are used in special region, and length 500 mm bricks are used in other region.
4. The thickness and shape of new bottom refractory were optimized.
5. A reasonable scheme of scrap charging has been worked out.
6. A reasonable power supply curve was established.
7. A reasonable EAF lining preheating scheme has been worked out.
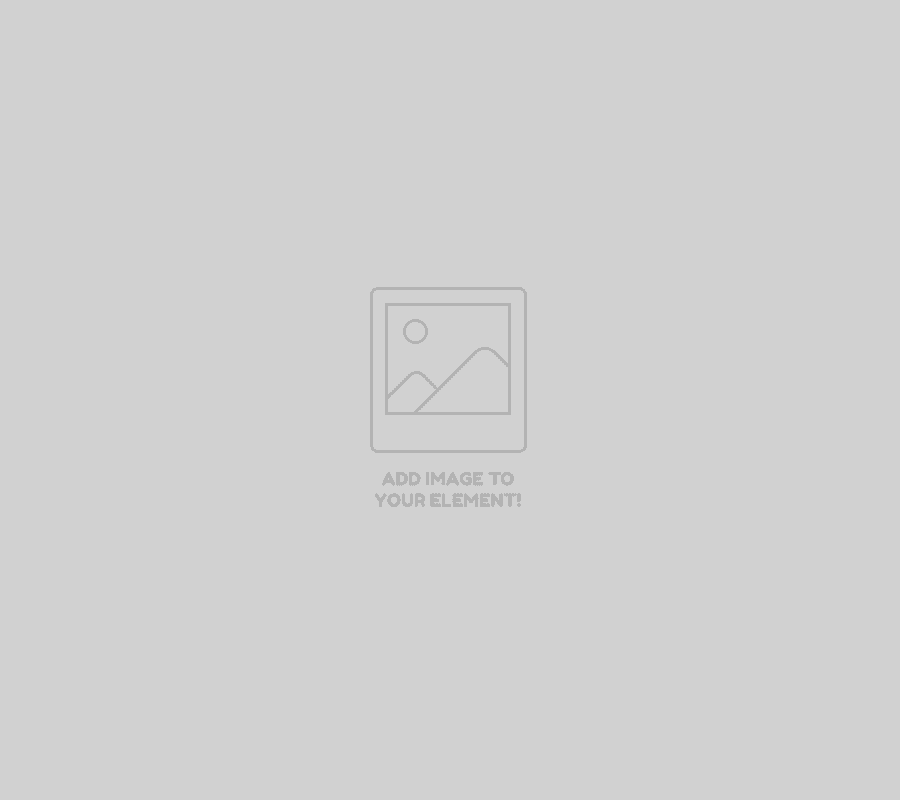
Team division of technical team
1. The steelmaking team is responsibleto optimize the production process again and formulate the corresponding scheme for Party A’s EAF.
2. Be responsible for the optimization of EAF bricks-construction technology.
3. Be responsible for guiding correct operation skills to workers on the site.
4.Trial period: Our first EAF lining was put into operation on September 18, and the second EAF lining was put out of production on October 15 in the morning.
- Comparison table of trial results and previous historical use results:
Supplier |
A |
B |
C |
Xingding |
Maximum life of EAF lining in history(Heat) | Center block life for EAF cover(Heat) | Technical support effect (Heat/shift) |
312 (one-time repair of slag line brick midway) | ≦174次 | max17 |
280 (one-time repair of slag line brick midway) | — | — |
260 (one-time repair of slag line brick midway) | — | — |
380 (Non-stop) | 400 | 18 |
- Comparison of other relevant technical indicators before and after technical service:
No. |
1 |
2 |
3 |
4 |
5 |
6 |
7 |
8 |
Index comparison | Before service | After service |
Lining life (Heat) | Max150 in history | 380 |
Life of EAF center block (Heat) | Max70 in history | The first one 250 |
Power consumption (kWh/T) | 420 | 370 |
Electrode consumption (kg/T) | 1.6 | 1.3 |
TTT(Min) | 48 | 40 |
Monthly change times of EAF lining (Time)) | 3—4 | 2 |
Furnace change duration (Hours) | 12-16 | 10 |
Monthly output (t/m) | 45000 | 60000 |
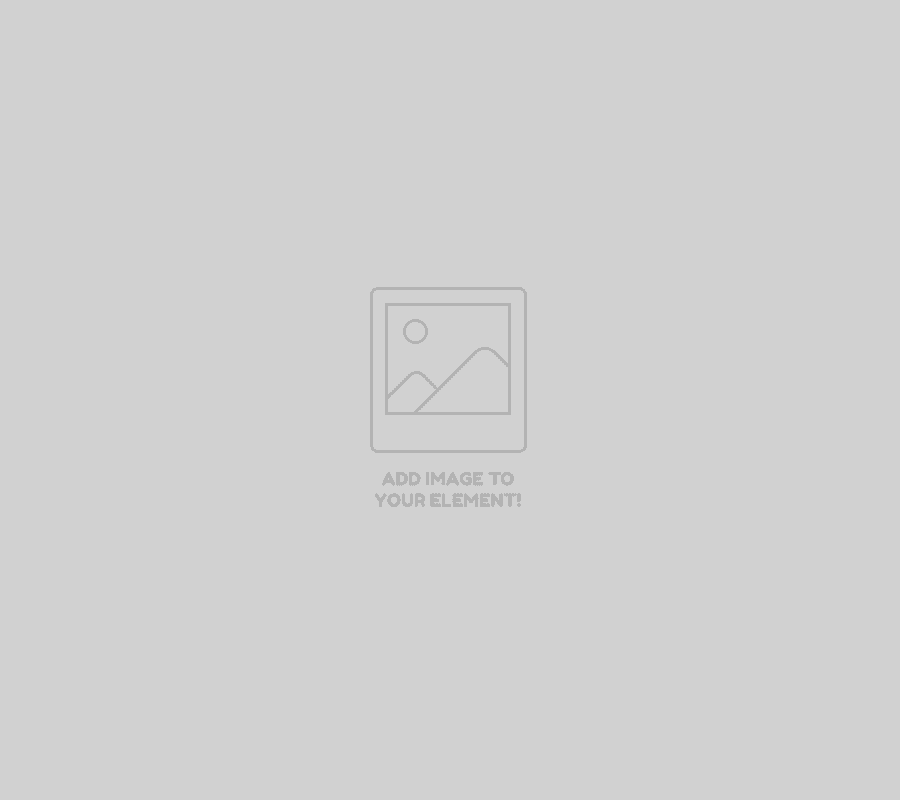
Summary
1. Through optimization of steelmaking process, including optimization of new EAF lining preheating, oxygen supply, slag making, power supply curve, and optimal hot heel, current comprehensive production capacity is 60000 tons / month, future output will be hugher than 6000t/m, but due to the shortage of Anshan scrap supply, sometimes it is forced to stop production;
2. under a good quality refractory, we optimized laying type of refractory , avoided electrode fracture when charging the block, and electricity consumption is significantly reduced comparing with before, but there is still great room for improvement. If scrap management is strengthened, the life of EAF lining can reach more than 400 heats. The previous two EAF linings killed 32 hours of production time. According to average outpup 30 heats per day and single output 80 t/h, company can raise output of 3200 tons according to EAF lining life reaching 380 times.
3. Help to improve slag-making process and power supply process, and the life of EAF center block has been greatly enhanced. However, it is still difficult to promote the life to thousands times due to the use of low-grade corundum. If high-grade corundum is used, the life can reach more than 1000 Heats.
4. If process is further optimized and the overall management of equipment and production is strengthened, EAF should reach designed capacity soon.The consumption of each index decreased evidently.
5. The production efficiency has been significantly improved, and the production capacity has been increased by more than 30%.
6. The comprehensive economic benefits have been significantly improved.
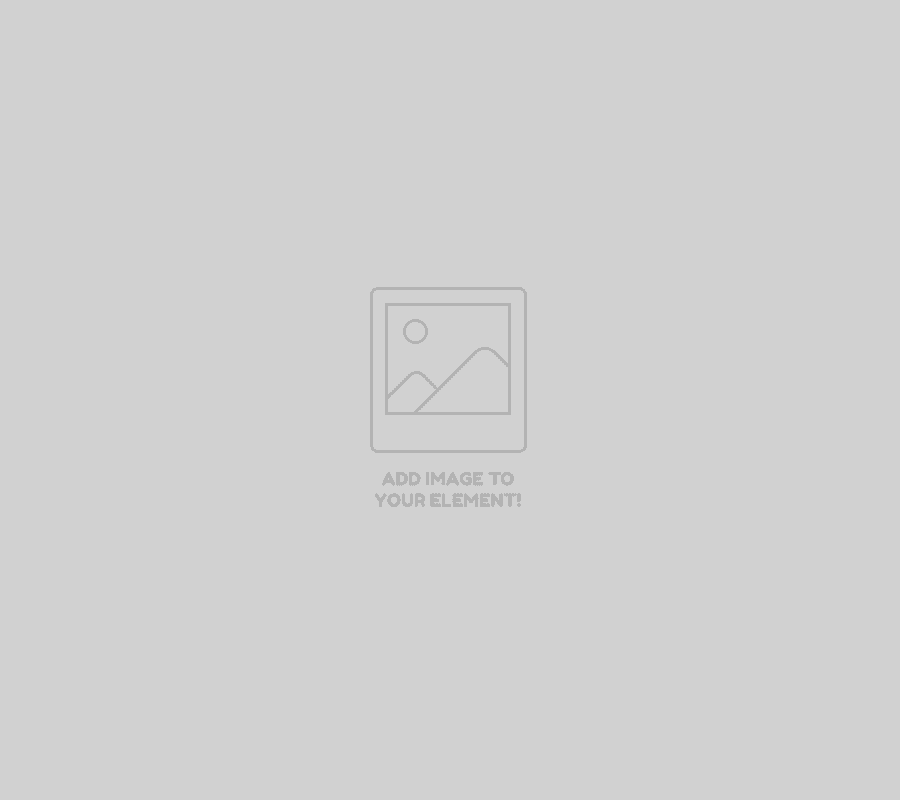