Technical service summary for YongHang Steel Plant in Chongqing
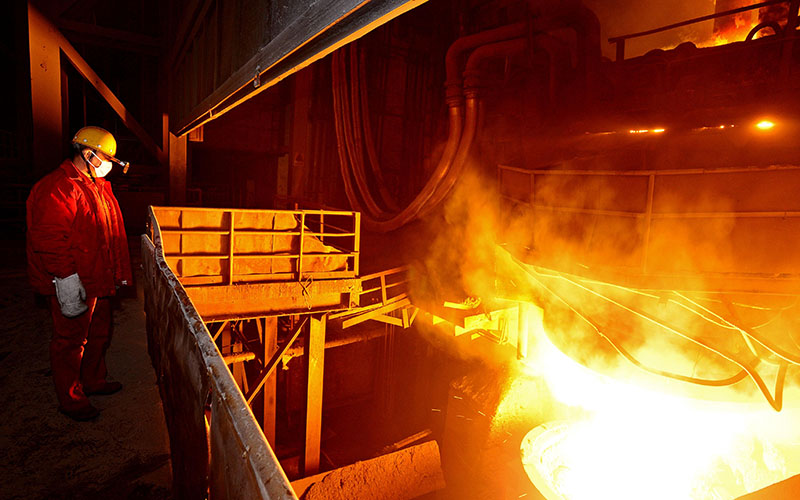
Preface
The technical team has gotten an agreement with Chongqing Yonghang Steel Co., Ltd. to implement a hot trial of a set of magnesia carbon bricks and related refractory auxiliary materials for a complete ling service period in Chongqing Yonghang 80T Consteel EAF, as well as magnesia carbon bricks and related auxiliary refractory for a ladle lining. Yonghang steel plant (Party A) required that the use life of our EAF magnesia carbon bricks and ladle carbon bricks must exceed the use life of previous refractory manufacturers, and demanded minimum service life of carbon brick forEAF is more than 350 heats, and the ladle is 105 heats. Yonghang steel plant has qualification which equipped with the equipment. The personnel’s operation level is relatively low, and the process optimization needed to be further improved.
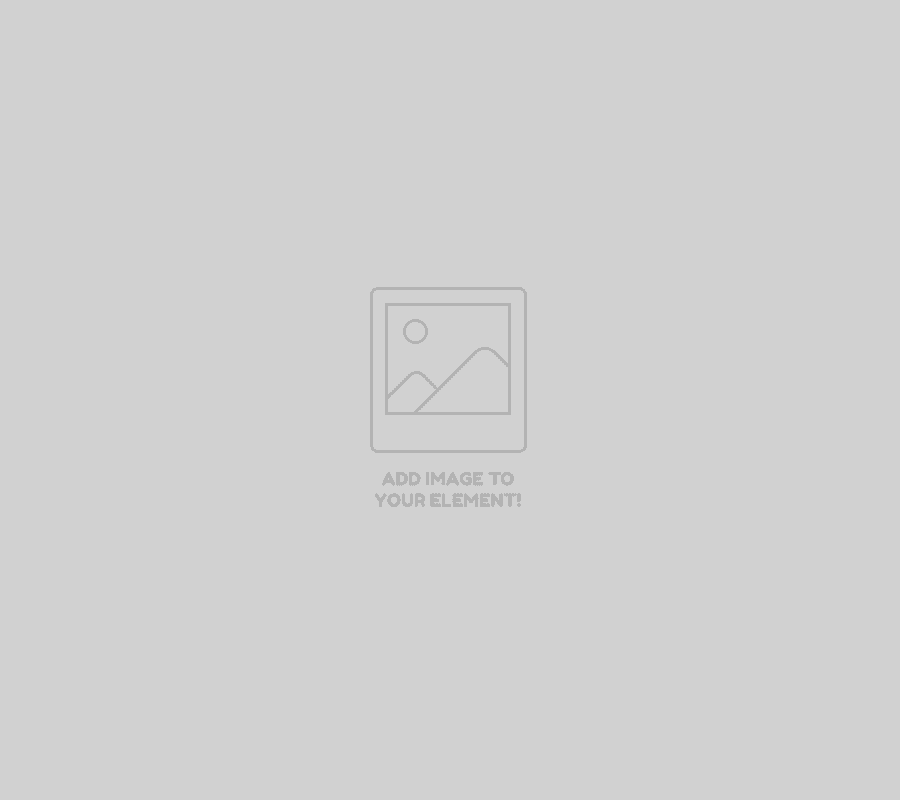
Production status of Yonghang at that time
1. The yield is low, not reaching the designed yield.
2. High power consumption.
3. The lining life is short.
4. The life of center block of EAF was very low.
5. High cost.
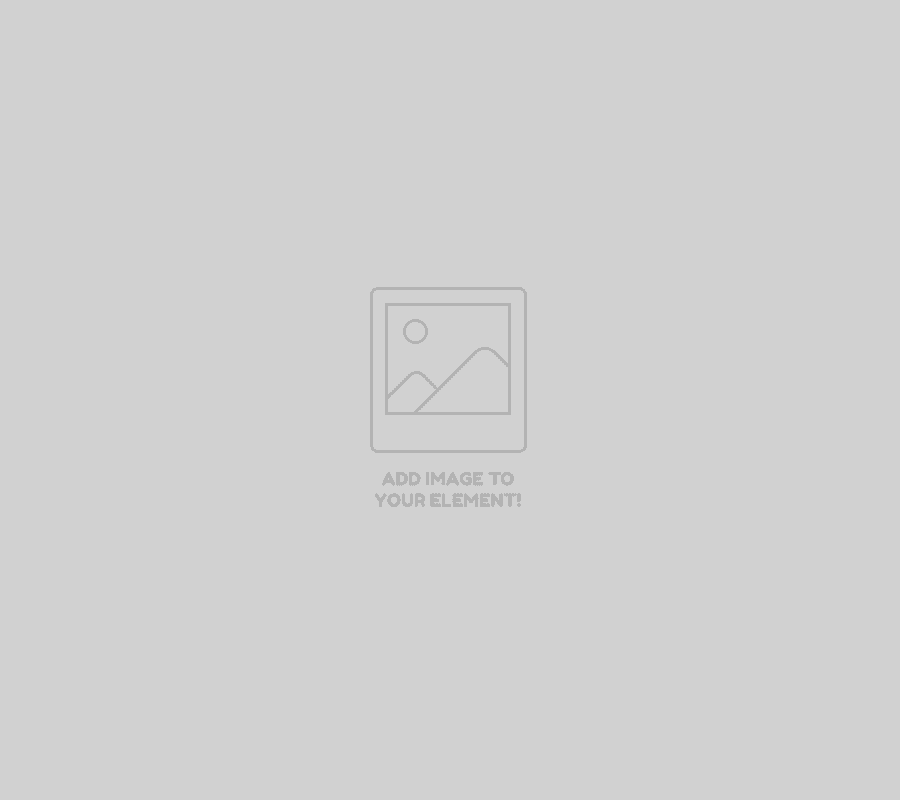
The technical support team involved
1. Be responsible for communication and coordination with General Manager and Purchasing Department of Party A.
2. The steelmaking team was responsible for products quality of EAF and LF and CCM and rolling mill of Party A, re-optimizing production process and formulating corresponding plans.
3. Guided and supervised the optimization of furnace and ladle lining-construction process.
4. Be responsible for the formulation of EAF ,LF ,CC process. and guided correct operation skills of workers in the site.
- Completion of assessment indicators. After 10 days of online use, the effect is compared with the best level in history:
Supplier |
A |
Xingding |
Maximum using life of carbon brick for EAF (Heat) | Maximum lining life for ladle in history | monthly output Before and after | Remark |
278 | 94 | 57000T | Highest in history |
354 | 114 | 83480T | May,2019 |
- Use summary:
1. In this test, technical team optimized refractory making process, the slag line brick erosion was uniform, the erosion rate was significantly reduced, the furnace slope erosion speed was also greatly delayed, and the refractory life was significantly improved.
2. in this experiment, we optimized slag foaming process, and the service life of refractories was well developed.
3. Due to the use of high-quality ramming materials, the erosion of furnace slope was very slow, the times of lining furnace slope were reduced, and the consumption of ramming materials in the later stage of furnace lining decreases suddenly, which greatly reduced downturn time; the production capacity was improved indirectly.
4. The Offline minimum residual thickness of EAF bricks were 200 mm, life will be about 500 heats if lining was used normally .
5. The ladle brick was not digged and repaired in the process, but replaced air permeable brick midway. The service life has reached 114 times. If the ladle brick was excavated and repaired, the life will be longer.
6. The comparison of the basic data in TABLE-1 shows that the final use results met the requirements of the agreement and were fully affirmed and recognized by Party A.
- Comparison of other relevant technical indicators before and after technical service:
No. |
1 |
2 |
3 |
4 |
5 |
6 |
7 |
8 |
9 |
10 |
Index comparison | Before service | After service | Remark |
Lining life (Time) | Max 278 heats in history | 380heats | — |
Center block life for cover (Time) | Max 200 heats in history | The first one 1394 heats | Up to 2780 times |
Power consumption (kwh/T) | 380 | 353 | — |
Electrode consumption (kg/T) | 2.1 | 1.21 | — |
TTT (Min) | 41 | 37 | — |
Monthly change times of EAF lining (Time)) | 3—4 | 2 | — |
Monthly change times of EAF lining (Time)) | 12-16 | 8 | — |
Monthly output (t/m) | 57000 | 83480 | — |
Consumption of ramming material for furnace slope (t/round) | 28 | 5 | — |
Gunning times of slag line (time/round) | 30 | 12 | — |
Afterwards, we have established a long-term cooperative relationship, and on this basis, local indicators have been greatly improved, reaching the leading level of peers.
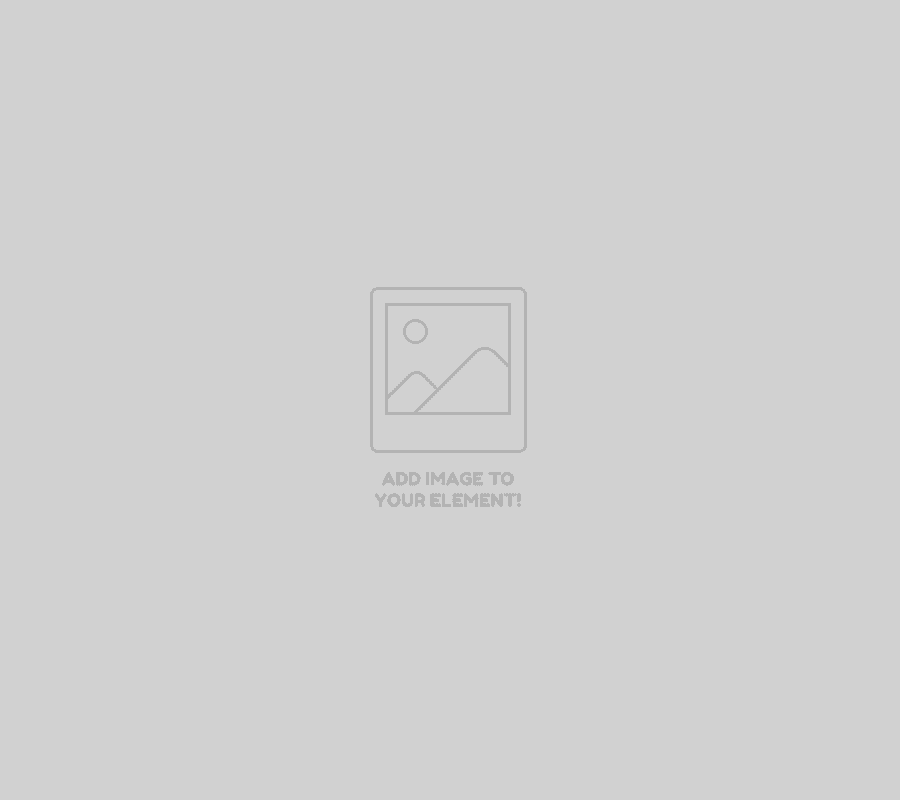
Conclusion
1. Through the optimization of steelmaking process, including the optimization of new furnace lining preheating, oxygen supply, slag making, power supply curve, and the best hot heel, production capacity and refractory life were greatly improved.
2. Under good refractory quality, combined with steel-making process, the overall life of refractory (furnace lining, ladle lining, etc.) was increased synchronously; the life of center block for cover was increased in series, up to 2800 heats, and it was used for three months.
3. The consumption of each index decreased obviously.
4. The production efficiency has been significantly improved, and the production capacity has been increased by 46.5% compared with former.
5. The comprehensive economic benefits have been significantly improved.
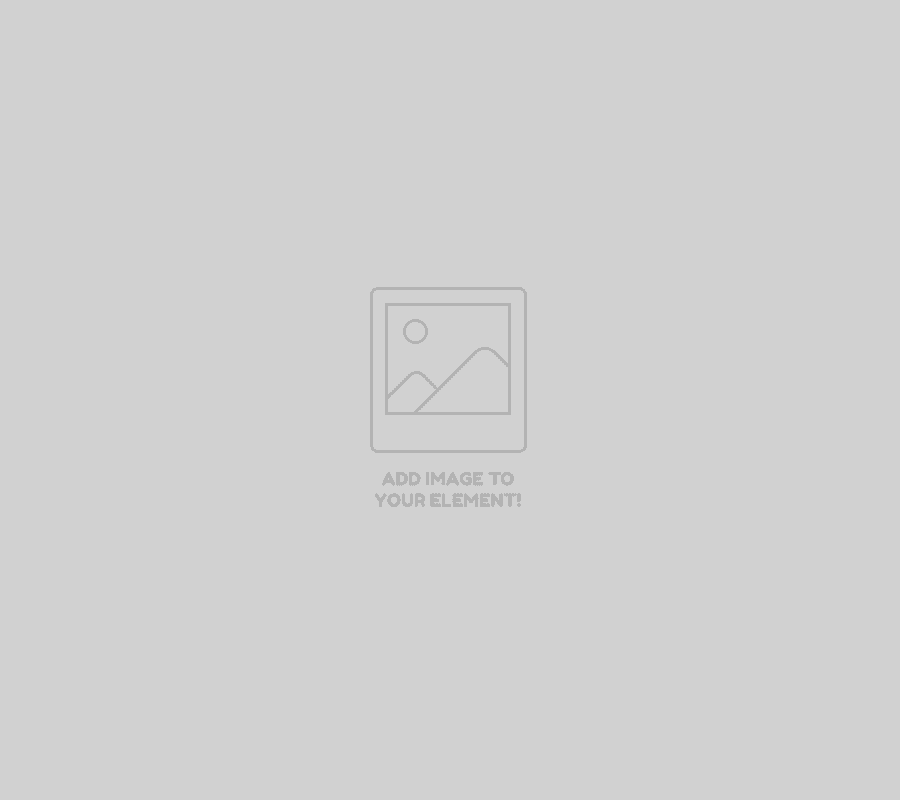