Technical service summary for Rongxing (Fujian) Special Steel Co., Ltd
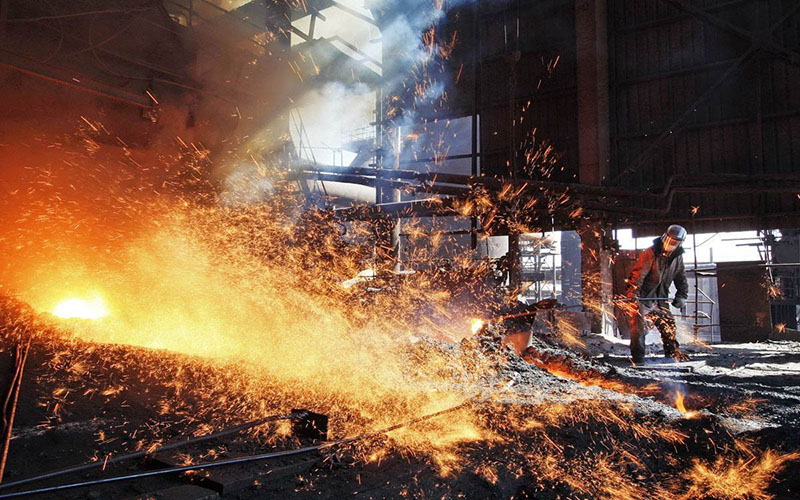
Preface
The technical team has gotten an agreement with Rongxing Steel Co., Ltd. to conduct a hot test of a complete set of magnesia carbon bricks and related refractory auxiliary materials for a complete ling service period in Chongqing Rongxing 70T Consteel EAF on Oct 29, 2019. as well as magnesia carbon bricks and related auxiliary refractory for a ladle lining. Rongxing steel plant (Party A) required that the use life of our EAF magnesia carbon bricks and ladle magnesia carbon bricks must exceed the use life of previous refractory manufacturers, and demanded minimum service life of magnesia-carbon brick for EAF is more than 350 heats, and the ladle is 84 heats.
The equipment condition of Rongxing steelmaking plant has a large room for improvement, but the EAF and LF operation level of on-site personnel is low. There are many problems on power supply system, slagging process, oxygen supply system, rationality of oxygen lance and carbon lance installation, lining masonry process, etc. the equipment management is not in place, and the scrap treatment and classification management are far from the requirements of high output. After our on-site observation and investigation, we made a detailed analysis of the whole production process and on-site operation, and formulated the corresponding improvement scheme.
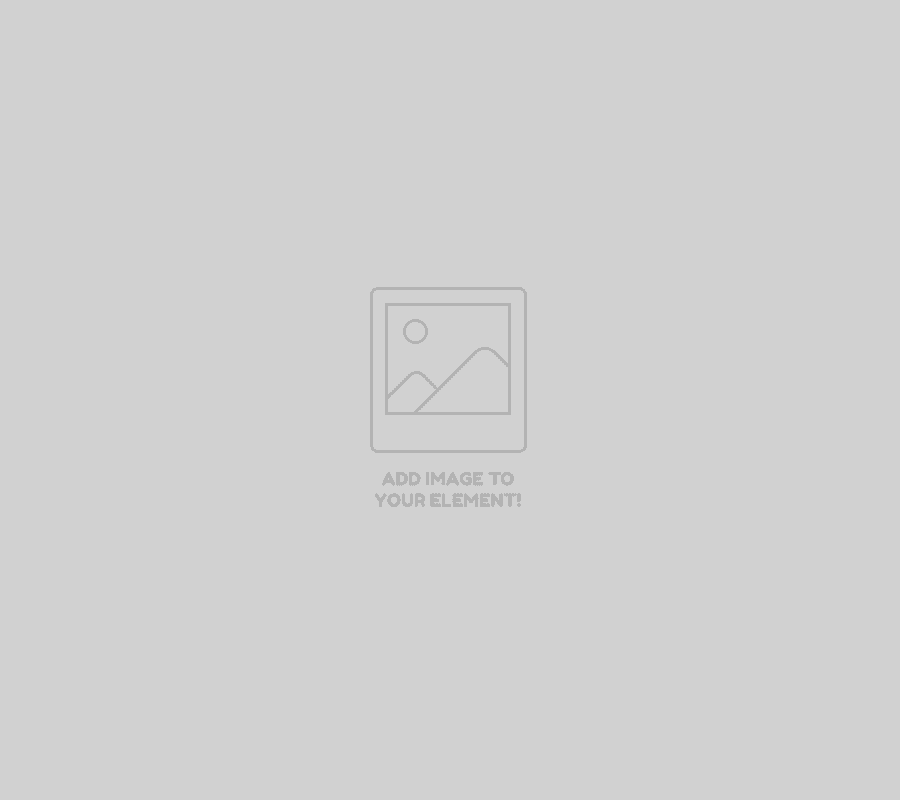
Present Situation
一、Basic equipment configuration of Rongxing Mini mill:
1.EAF, Furnace shell diameter 5.6m, transformer capacity 50MVA, tapping capacity 83t
2.LF, Transformer capacity 12.5MVA for safe full-load 95T, with single argon-blowing in EAF bottom.
3.CCM, With 6 machines and 6 strands
二、Production status of Rongxing at that time before techical team support:
1. The output: Monthly output 30000t/m, annual output 280000t/y
2. Power consumption. Total 570kwh/t. EAF 430kwh/t, LF 63kwh/t
3. EAF lining life: max 220heats, average 160heats
4. The life of center block of EAF: average 350heats.
5. Using life of ladle lining: average 50, max 84 heats.
6. Production cost: 1050CNY/t.
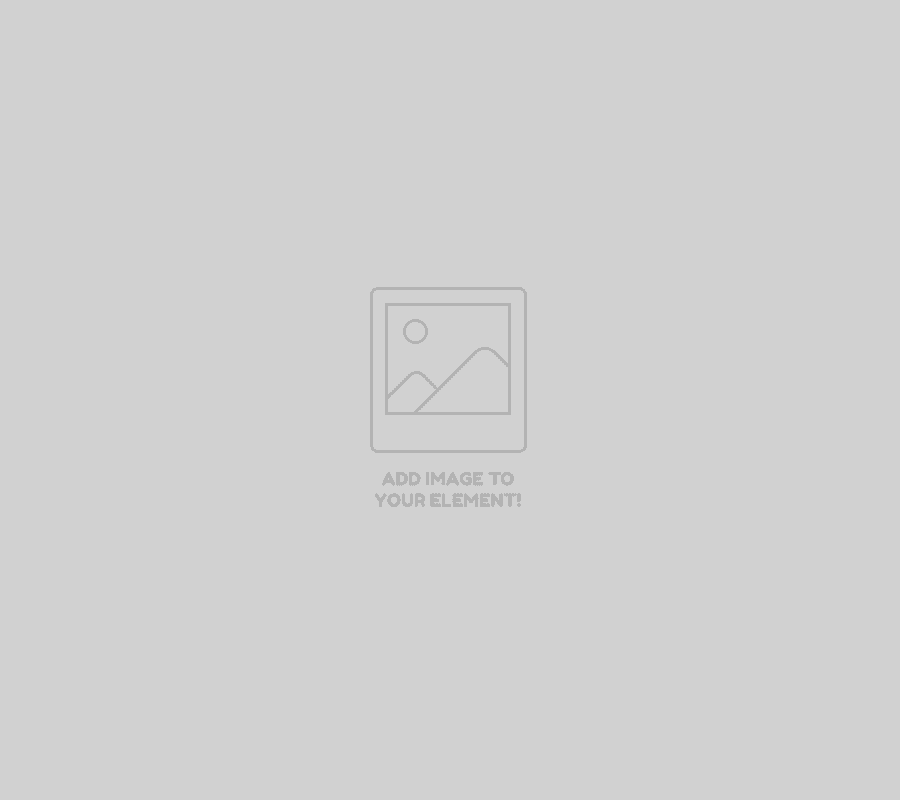
Improvement measures
1. Restore the oxygen lance between the horizontal charging inlet and EBT, and readjust the installation angle of all oxygen lance.
2. a carbon gun was added between the 2# electrode and EBT to ensure the need for foaming slag in the whole process.
3. In order to make refractory consume synchronously and finally prolong the furnace lining life, the local strengthening masonry method in hot spot area is adopted. Some 600 mm bricks are used, and 500 mm bricks are used in other locations.
4. The thickness and refractory shape of the bottom of the new furnace are optimized.
5. Reasonable scrap charging scheme and power supply curve are established.
6. Optimize and adjust EAF — LF– CCM smelting process and temperature.
7. A reasonable EAF lining preheating plan was made.
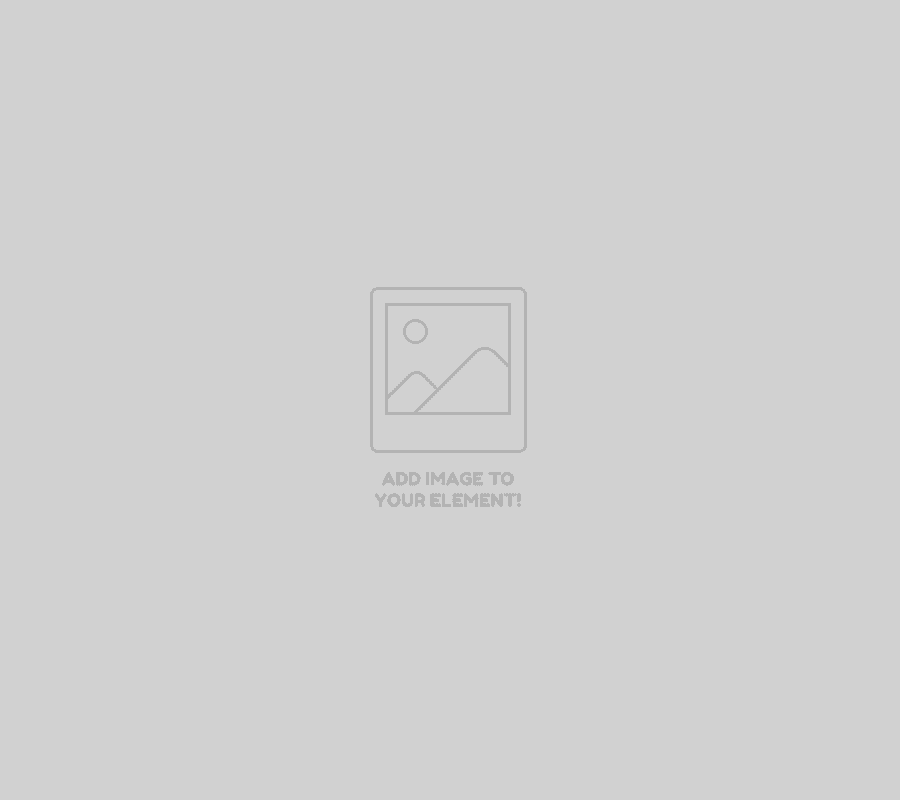
The technical support team involved
1. Steelmaking team is responsible for Party A’s EAF-LF-CCM production process optimization, and re-optimize the production process, and formulate the corresponding scheme.
2. Responsible for the optimization of electric furnace masonry process and the scientific and reasonable design of furnace type.n.
3. Be responsible for guiding the correct operation skills of on-site workers.
4. Trial period: Our first EAF lining was put into operation on October 29, and the second EAF lining was put into operation on November 15, morning.
- Comparison table of trial results and previous historical use results:
Supplier |
A |
B |
C |
Xingding |
Maximum life of EAF lining in history(Heat) | Center block life for EAF cover(Heat) | Technical support effect (Heat/shift) |
312 (one-time repair of slag line brick midway) | ≦174次 | max12 |
280 (one-time repair of slag line brick midway) | — | — |
260 (one-time repair of slag line brick midway) | — | — |
617 (disposable) | 1286次 | 18 |
- Comparison of other relevant technical indicators before and after technical service:
No. |
1 |
2 |
3 |
4 |
5 |
6 |
7 |
8 |
9 |
Index comparison | Before service | After service |
EAF Lining life (Heat) | Max 230heats in history | 554heats |
Center block life for cover (Heat) | Max 348 heats in history | The first one 2394 heats |
EAF power consumption (kwh/T) | 387 | 343 |
LF power consumption | 68 | 38 |
Electrode consumption (kg/T) | 1.9 | 0.94 |
TTT (Min) | 58 | 40 |
Monthly change times of EAF lining (Time)) | 3—4 | 2 |
Change duration of EAF lining (Hour)) | 6 | 3.5 |
Monthly output (t/m) | 38000 | 60000 |
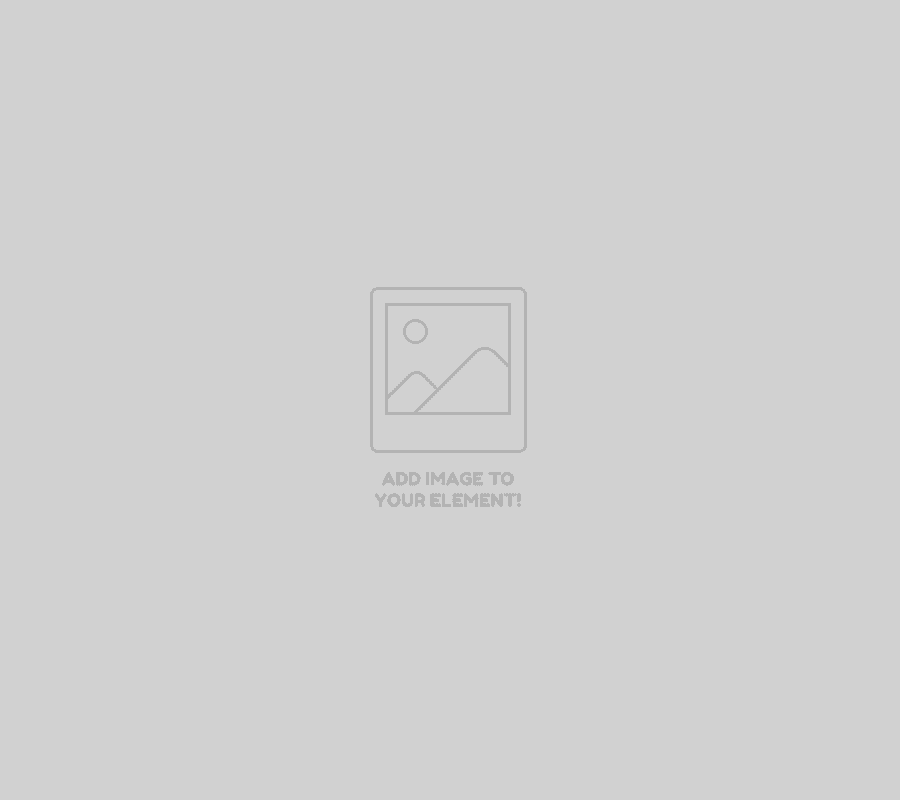
Conclusion
1. Through the optimization of steelmaking process, including the optimization processes of new furnace lining preheating, oxygen supply, slag making, power supply curve, and the best hot heel, According to the current comprehensive production capacity of 60,000 tons / month, in the early stage, due to the shortage of scrap supply in Rongxing steel making plant, it is sometimes forced to stop production. In the later stage, the scrap supply is normal, and the monthly output is basically stable at about 75,000 tons.
2. Under the premise of good quality refractory, we optimized the refractory type of EAF, and the power consumption lowered much than before, If the scrap management is strengthened, the service life of EAF lining can reach more than 800 heats. The previous 2sets of EAF lining wasted 32 hours of production time due to repairing bricks. According to the average daily output of 30 heates and the output of 80tons/heat, our company can increase the output of ,8400 tons according to 580 heats life.
3. Help to improve slagging process and power supply process, the service life of center block life of EAFhas been greatly improved, Its center block life is made of low grade corundum, so it is difficult to increase its service life to thousands of times. If high-grade corundum is used, it will be easier to have a service life of more than 2000 heates.
4. If we further optimize the process and strengthen the overall management of equipment. The safety, stability, high efficiency and sustainability of production will be achieved.
5.The production efficiency has been significantly improved, the production capacity has been increased by more than 50%, the production cost has been reduced to 688CNY/ton, and 362CNY/ton of steel has been saved.
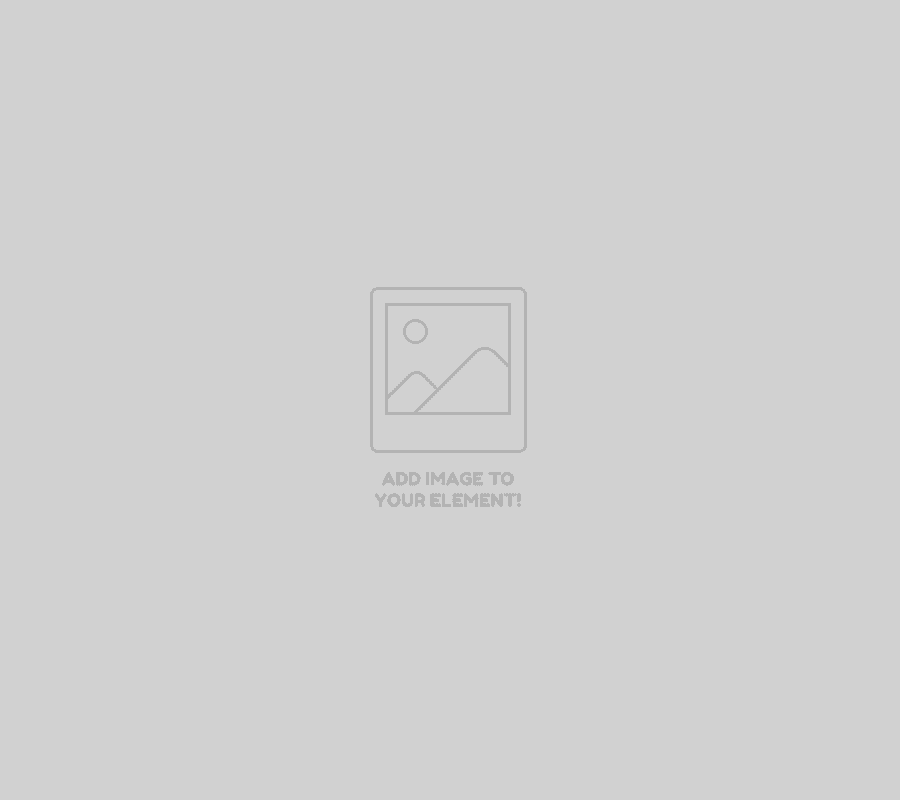
Win-win cooperation plan
As EAF steelmaking is a high energy consumption and high consumption production mode with scrap as main raw material, it brings great challenges to the production and operation of mini mill line. In order to improve the competitiveness of short process steelmaking plants in the same industry, we optimize and change the production and smelting process in steelmaking plants, focusing on the process flow of steelmaking plants, reducing production manufacturing costs, and expanding living space of EAF steelmaking plants At present, our company has professional refractory team and professional steeling-making team with 4 senior steelmaking engineers, 8 senior steelmaking technicians and a group of experienced furnace directors who have been engaged in EAF steelmaking for decades. We will give all-round technical support on the cooperative steelmaking plants, and implement some process adjustment and optimization without increasing the cost of steelmaking plants, In order to reduce the production and manufacturing costs to maximum, the company’s performance cases show that process cost has been significantly reduced through cooperation with other domestic steel plants to provide technical support, our future goal is to take the EAF steelmaking plant as a platform, both sides work together to create a benchmarking enterprise in the same industry.
With the principle of high efficiency production and sustainable and stable development, on the basis of stabilizing the production of EAF, we should make some slight adjustments to the original design that restricts the safety production and reduces the production cost, or introduce some new auxiliary technologies, gradually and timely introduce new low-cost, practical, necessary technologies, so as to optimize the production process to the maximum extent, which is our ultimate goal that we cooperate together with “Safe production, high quality service, efficient operation, high output and low consumption” principle.
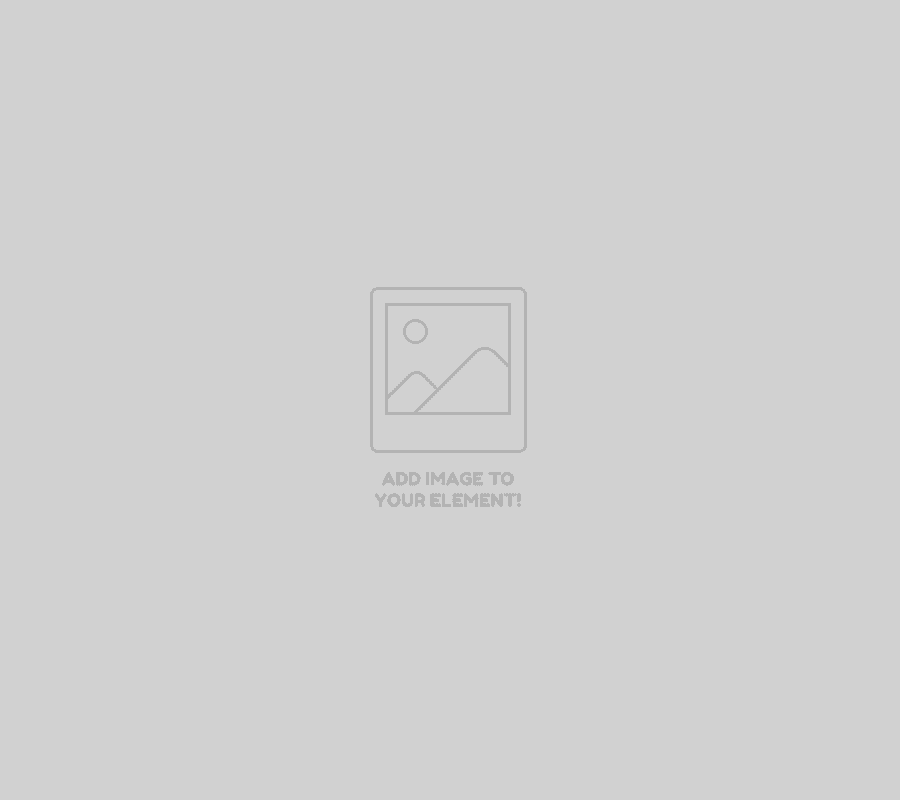