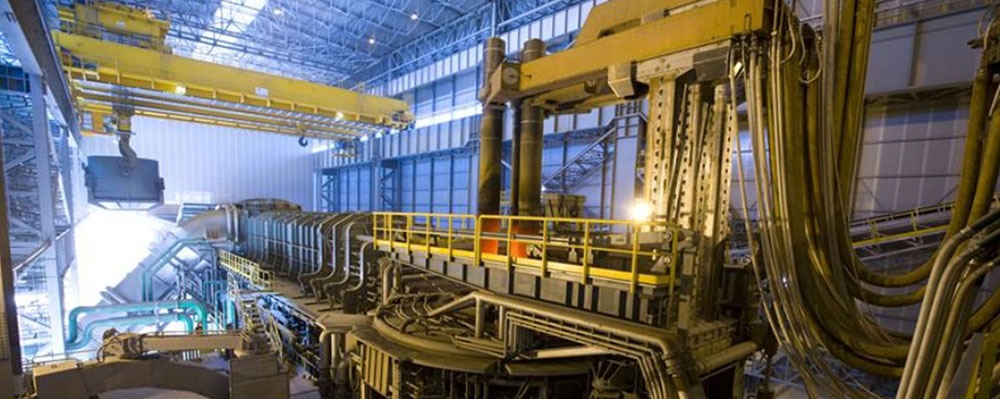
Preface
Chinese government banned the intermediate frequency furnace steelmaking production line Since 2016, a large number of UHP EAF- LF-CCM- Rolling mill short process production lines have been generated by capacity conversion.
In 2018, the construction of EAF has entered a climax, a large number of EAF plants have been put into operation continuously, so the demand for scrap is soaring; the price of scrap raw materials is rising, and the price of finished products is falling. The EAF industries are faced with the dilemma of high cost, the profit space of finished products is sharply compressed, and many top charging EAF plants are in a state of loss. In order to cope with the depressed iron-steel market, make sure that enterprises can continue to survive and have stronger market competitiveness, the energy-saving EAF has become the first choice and has been favored by owners especially.
Compared with the continuous charging Consteel EAF, the defect of high cost of top charging EAF is particularly prominent, which has lost the market competitiveness. Many of the top charging EAF factories in operation have been transformed into more energy-saving horizontal continuous charging EAF(Consteel) to further tap the cost potential and reduce the production cost to the maximum; some of the newly building factories directly are build a high configuration of the Consteel EAF or the more respected and energy-saving quantum EAF in the world, in order to achieve the lowest production Cost.
In such a situation, steel industry in China, especially short process enterprises in the building materials industry, the Consteel EAF has become the main stream in the industry. At the same time, with the popularization of the Consteel EAF, its smelting process and refractory material process have been made great progress, all aspects of the technology are becoming mature, which has completely subverted the steelmaking mode of traditional EAF , and is a great revolution and a new milestone of short process steelmaking.
Therefore, for original top charging EAF plants, the best feasible solution to get rid of the dilemma is to modify it to a Consteel EAF on the basis of the original top charging EAF, which is the most effective, the least investment and the most significant method for cost reduction; it can increase the production capacity by more than 40%, and at the same time achieving the goal of reducing the comprehensive production cost, which is also the only shortcut.
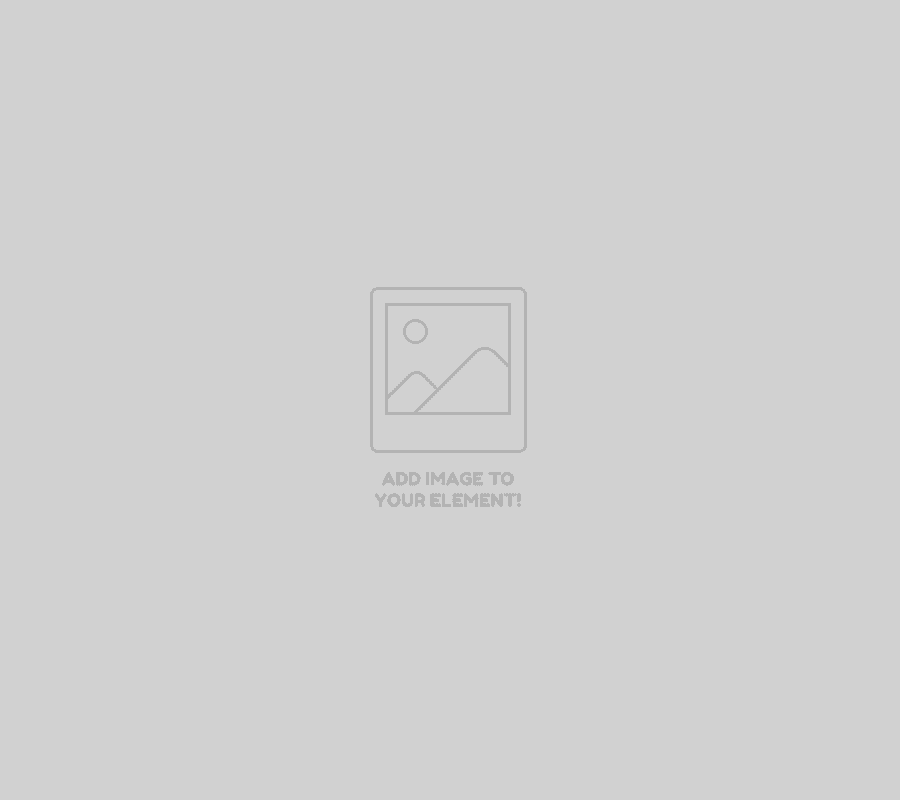
The advantages of EAF continuous charging compared with traditional top charging EAF on main process and technical indexes
1. TTT is shortened by 10-30 minutes;
2. Increase tapping capacity by 10%;
3. 80-100kwh can be saved per ton of steel;
4. The capacity of EAF transformer is about 20% – 40% smaller, which can reduce 5% of the electricity charge for capacity increase;
5. The time utilization rate of transformer is high, which is more than 90%;
6. Graphite electrode consumption reduced by 20-40%;
7. 5% reduction in refractories;
8. The yield of scrap was increased by 1.5-2%, and the yield reached 94%;
9. Production capacity increased by more than 40%;
10. In the preheating process, all the oxyhydrogen compounds are burned out, the molten pool keeps boiling all the time, which reduces the gas content in the steel and improves the quality of the steel.
11. The arc is always in the state of foam slag, the arc is particularly stable, and the interference of the power grid is greatly reduced, so the SVC device is not needed.
12. The amount of smoke and dust per ton of steel decreased from 17kg-20kg to 11kg;
13. The amount of CO released per ton steel decreased by 20-30%;
14. The dust content in the production site is less than 10mg / m3;
15. The emissions of dioxin and CO meet the emission standards of developed countries.
16. The power of blower is reduced by 30-40%.
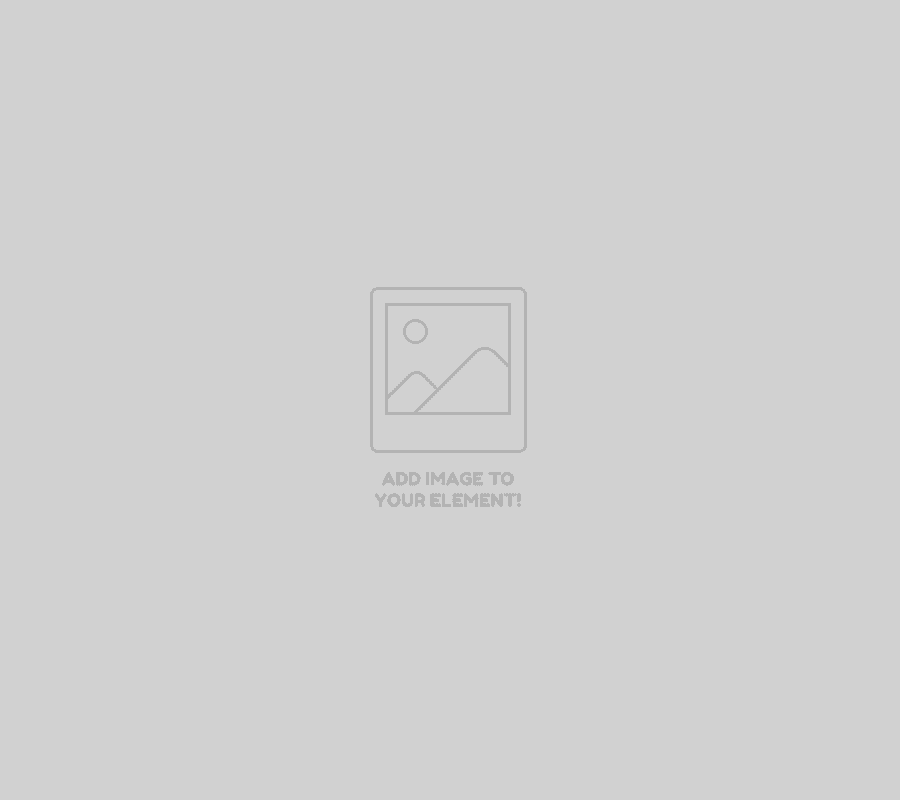
The cases of improving production capacity for several domestic Consteel EAFs by technical team
Although China’s EAF plants have been under the pressure of market competition to build or transform the original top charging EAF into a Consteel EAF, there is a common weakness: in China, there were few Consteel electric arc furnaces previously. so when Consteel EAF became the main stream for cost reduction, most of the factories remained in the concept of top charging EAF for the smelting process of Consteel EAF in the exploration stage, except for a few well-designed and well-equipped factories could reach capacity designed within a short time after being put into operation, The others, due to objective (inherent design defects) or subjective (operators do not have a good understanding on the basic principles and smelting process of the Consteel EAF), couldn’t reach the capacity designed for a long time; our technical team grasps this Opportunities providing strong technical support for these unqualified Consteel EAF factories. Starting from optimizing steel-making process and refractory process, we focus on strengthening raw material management especially scrap, standardizing operation process, optimizing power supply curve and other powerful measures, so these factories can reach the designing capacity in a short period of time, each index can reach the industry standard, and some of indexes are in the leading position in the industry.
Our technical team has made Consteel EAF plants with abnormal production to upgrade to the designed standard, through optimizing the smelting process, refractory process and partial equipment modification (all scrap smelting). and some consumption indexes become the benchmark of the industry.
Now, the consumption index data of three representative Consteel EAF plants with different capacities ,which our team has served are summarized as follows. Each index has reached a higher level in the domestic industry, which has created considerable profits for the enterprise. Meanwhile, made the indexes of Consteel EAF compared with the top charging EAF with the same capacity that are advanced in China respectively, let the readers understand clearly and intuitively over the difference between the two kind of EAFs. From the perspective of comprehensive economy, Consteel EAF is far superior than top charging EAF in comprehensive cost, which has great industry promotion value.
- Comparison of consumption indexes of Consteel EAF and top charging EAF:
No. |
1 |
2 |
3 |
4 |
5 |
6 |
7 |
8 |
9 |
10 |
11 |
EAF Capacity | 60T | 80T | 120T | |||
Charging Mode | Top charging | Continuous charging | Top charging | Continuous charging | Top charging | Continuous charging |
Tapping Quantity(T) | 65-70 | 65-75 | 80-90 | 85-95 | 125-130 | 125-135 |
Scrap yield(%) | 86-91 | 90-93 | 88-91 | 90-93 | 88-91 | 90-93 |
Electricity(kwh/t) | 400 | 350 | 390 | 340 | 370 | 310 |
Electrode(kg/t) | 1.6 | 1.2 | 1.5 | 0.95 | 1.3 | 1.05 |
EAF Linning life(Time/set) | 420 | 480 | 450 | 550 | 450 | 620 |
Oxygen(m3/t) | 26 | 26 | 26 | 24 | 22 | 21 |
Lime(kg/t) | 35 | 35 | 35 | 35 | 35 | 30 |
Carbon powder(kg/t) | 24 | 20 | 22 | 18 | 22 | 16 |
MgO ball(kg/t) | 5 | 5 | 6 | 6 | 10 | 10 |
Carbon spheres(kg/t) | 1 | 1 | 1 | 1 | 1 | 1 |
Notes: 1. TTT of top charging electric arc furnace is 45 minutes to 60 minutes according to the capacity of transformer and auxiliary matching;
2. TTT of Consteel is 30 minutes to 45 minutes according to the capacity of transformer and auxiliary matching;
Summary:From the statistical data in the above table, it can be seen the remarkable effect and advantages of Consteel EAF compared with top charging EAF are as follows:
1. Shorten smelting time
2. Reduction of power consumption per ton of steel
3. Reduction of electrode consumption per ton of steel
4. Increase of scrap yield
5. Lining life greatly be improved
6. The comprehensive cost per ton of steel can be reduced by about 200 RMB
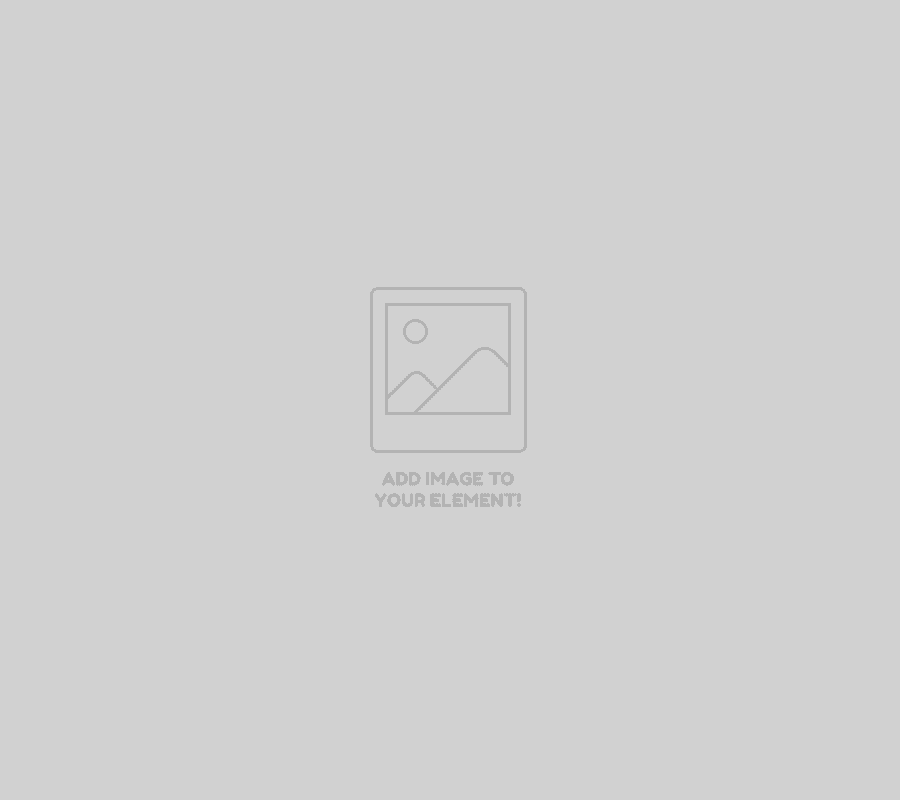
The technical team modified a 60T top charging EAF into a continuous charging case in China
This is a steel-making plant that our technical team modified the top charging EAF into a Consteel EAF. Our technical team also helped the plant to train the site personnel for operation, optimized the process and improved the production capacity. Now, the statistical data of actual production and the final benefit analysis are submited to you, so you can have a deeper understanding on the technical point of view described in this paper, and more intuitively reflect the modification of top charging EAF into Consteel At the same time, the feasibility and necessity of modifying top charging EAF into Consteel EAF are confirmed by the economic benefits brought by the capacity improvement and cost reduction before and after the modification.
- Index comparison before and after transformation:
NO. |
1 |
2 |
3 |
4 |
5 |
Index name | Top charging | Consteel | Price difference per ton of steel | Remarks |
Scrap yield(%) | 0.89 | 0.92 | 69CNY/t | 2300CNY/t(scrap price) |
Electric(kwh/t) | 410 | 350 | 36CNY/t | 0.6CNY/kwh(electricity price) |
Electrode(kg/t) | 2.1 | 1.2 | 27CNY/t | 30000CNY/t(electriode price) |
Lining consumption | 280 heats | 400 heats | 10CNY/t | — |
Wages of workers | 68CNY/t | 30CNY/t | 38CNY/t | — |
- Comparison of economic benefits:
The production duration is 26 days per month, the daily output of Consteel EAF is 36 heats / day, and the output per heat is 60 t/heat ; the daily output of top charging EAF is 22 heats / day, and the output of per heat is 60 t / heat.
1. Daily output of Consteel EAF: 36 heats / day×60 t/heat=2,160 t/d
2. Daily output of top charging EAF: 22heats / day×60 t/heat=1,320 t/d
3. Monthly output of Consteel EAF: 2160t/d×26d=56,160 t/m
4. Monthly output of top charging EAF: 1320t/d×26d=34,320 t/m
5. Capacity:(56160-34320)/34320=63.6%
- Analysis of annual economic benefit difference:
Based on production cost difference of 180 CNY/t offered by the table above , 56160t per month will be produced after modification.
Difference of monthly benefit: 180CNY/t×56,160t =10,108,800CNY
Annual benefit difference: 10,108,800CNY×12=121,305,600 CNY
- Summary:
Modification of 60 ton top charging EAF into Consteel EAF brings considerable economic benefits to the enterprise:
1.?After transformation, the production capacity increased by 63.6%
2.?Reduce cost by 180 CNY / ton
3.?Monthly profit increased by 10,108,800CNY
4.?Annual profit increased by 121,305,600 CNY
5.?About 12,000,000 CNY is invested in equipment transformation
6.?Investment of equipment manufacturing can be recovered in a month
7.?Investment of equipment modification only accounts for 1 / 10 of the annual net profit
Our technical team has successfully achieved the improvement through technical service time of within three months as shown in table-2, which is a very successful transformation case, further proving that Consteel electric arc furnace has incomparable advantages over top charging electric arc furnace. The transformation of top charging electric arc furnace into Consteel electric arc furnace has small investment, obvious cost reduction and quick effect. Short process steel enterprises at home and abroad have extremely commercial promotion value, early selection early benefit.
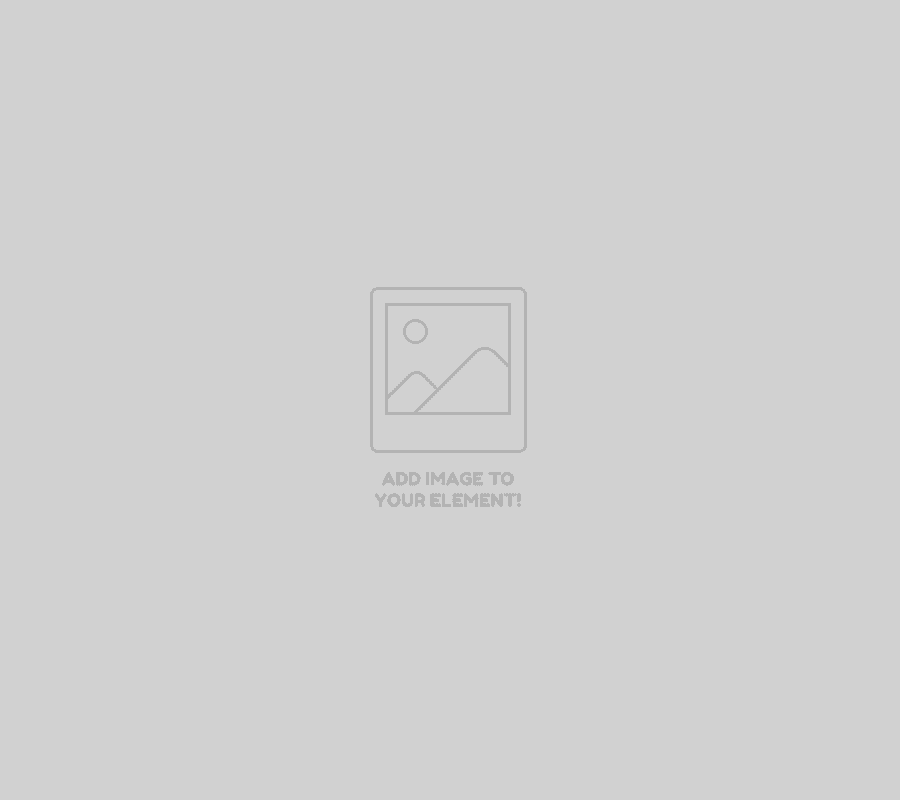
Related matters on top charging EAF to horizontal charging over the modification
- Need to increase equipment and equipment production and installation cycle
1. 1 set of horizontal charging system.
2. 2 sets of furnace upper shell and 2 sets of furnace cover.
3. 1 set of furnace weighing system.
4. Other old parts will be utilized.
5. The equipment manufacturing period is 75-90 days.
6. The installation period is 25-35 days.
- Technical service
1. Technical guidance for equipment installation.
2. Technical guidance for equipment commissioning.
3. Routine maintenance during equipment commissioning.
- Personnel training
1. Equipment operation and maintenance personnel training
Trainees: equipment operators and maintenance personnel.
Training content: introduction, installation and maintenance of continuous charging device.
2. General electric control operation and maintenance training of equipment
Trainees: operation and maintenance electrician and maintenance personnel.
Training content: principle, operation and maintenance of electrical equipment of scrap continuous feeding device, including introduction of inverter knowledge.
3. Process operation training
Trainees: process technicians and furnace operators
Training content: continuous scrap feeding device process.
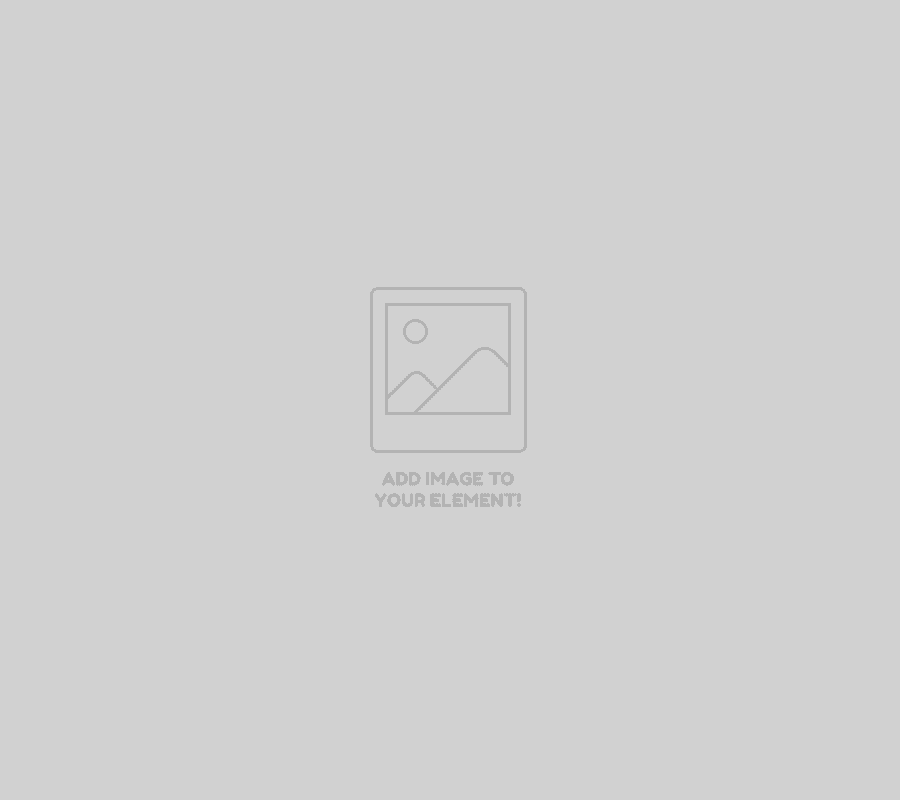
Technical team service for process optimization and capacity improvement
- Smelting process optimization
Trainees: process technology in charge, shift foreman and furnace foreman.
Training contents: smelting process – scrap management, loading process, continuous feeding process, power supply process, foaming slag process.
- Refractory process optimization
Trainees: process technical director, site technical director, site refractory director and operators.
Training content: Refractory – laying process, ladle- laying process, EBT quick replacement process, etc.
- Refining furnace process
Trainees: process technology director and refining furnace manager.
Training content: refining furnace process optimization.
- Training cycle
According to the learning ability of local employees in the factory and the mastery of skills, the training period can be 3-6 months.
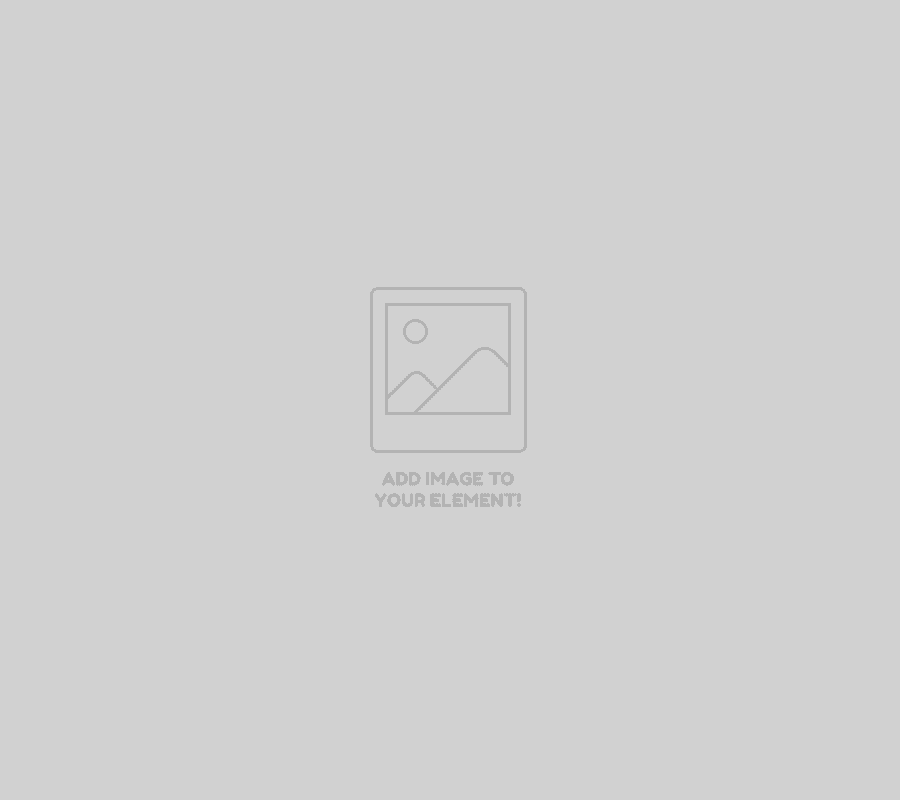
Conclusion
Our company is willing to use our excellent technical team to cooperate with foreign EAF plants in good faith to form a one-stop service from the modification scheme design, installation, commissioning, and finally promoting the output to the capacity designed through the site service by technical team , so as to truly achieve the goal of win-win B/W two sides.
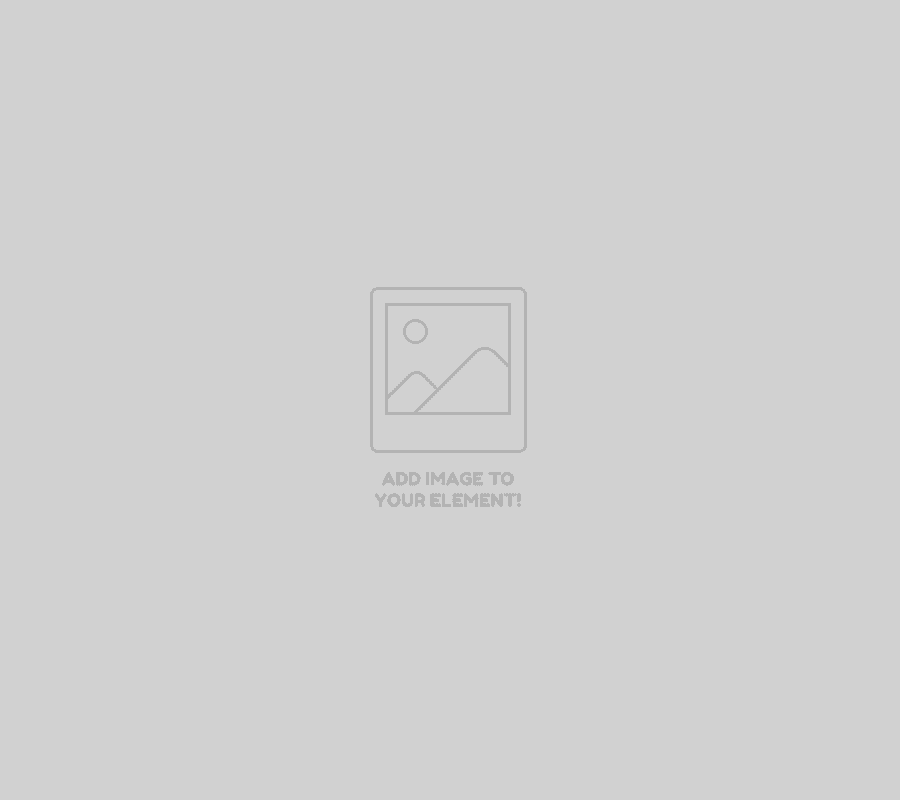